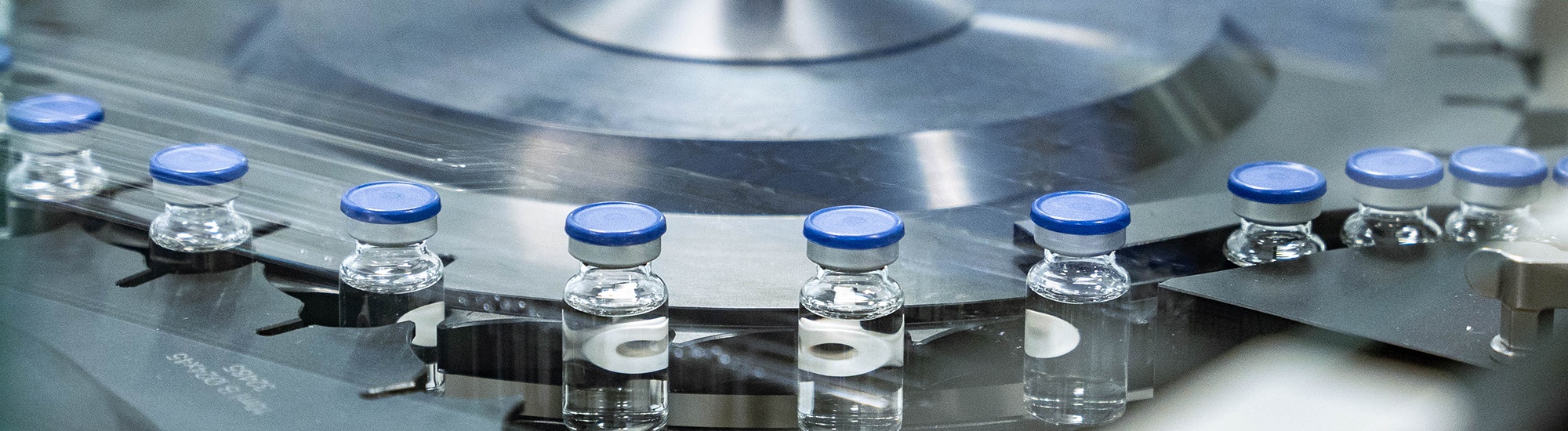
By: Aaron Bober Director, Engineering
If the Covid-19 pandemic taught us anything, it was to avoid coughing crowds and marvel at the remarkable speed of innovation. Whether mRNA vaccines to stop a pandemic or the rapid rise of cell and gene therapy to create personalized cancer cures, the rate of change is accelerating. The Covid-19 precedent also demonstrates that the Food and Drug Administration can move fast if needed.
Going forward, the first to market will be the first to get their manufacturing lines up and running. To meet the need for speed, we need to rethink the traditional design-bid-build path forward for engineering and construction. The design-assist approach is becoming increasingly popular worldwide, and it is easy to see why, as it blazes a faster trail to market. It is better for patients, and it is better for your bottom line. In fact, getting a drug to market first and fast will vastly improve the balance sheet more than the few percentage points you may save in competitive bidding.
During the pandemic, I worked with a significant player in the pharmaceutical market on a greenfield project to get new manufacturing lines up, running, and validated within 30 months. I firmly believe that we could only do that through design assist. I firmly believe that lives were saved because we could safely accelerate construction by approaching the problem of organizing the engineering and construction process differently.
It is the sort of paradigm shift in the industry that will generate fierce resistance, particularly in service to the biopharmaceutical industry, which is fundamentally built on managing risk. That same industry, however, can best serve its customers by getting to market faster. Design-assist is uniquely poised to succeed in pharmaceutical manufacturing in the Greater Boston region.
The Case for Design-Assist
The design-bid-build method is the norm for the architecture, engineering, and construction industry – regardless of whether you are building an office block or manufacturing space. Typically, engineering and construction represent two separate phases – the engineers and architects compile the construction (IFC) documents. Then the Construction Manager bids out for suppliers and trades to get the job done.
The competition for the job among suppliers and subcontractors helps keep costs competitive, which makes clients happy.
The downside comes from “change orders,” which can slow your construction timetable in several ways. First is the nature of equipment manufacturers, particularly in the pharmaceutical market, who will not necessarily craft bespoke equipment in a reasonable timeframe. Any idiosyncrasies between the IFC package and what gets delivered to the loading dock might lead to a change order to allow integration.
The second source comes from the trades and construction contractors, who often find that the IFC package might not reflect what is on the site when they arrive at work. One might also find that some subcontractors do not have as firm a grasp on the “design intent” of the engineering team, leading to decisions on-site that might lead to further problems down the line.
Both general types of change orders represent a fundamental disconnect between the architecture/engineering team and the subcontractors. When the design team revisits its plans, it shifts timetables further, which leads to increased labor costs and cuts.
The design-assist process begins with the design intent. Under the design-assist model, the architects and engineers develop about 60% of the detailed design, and the remaining 40% is completed with engagement from vendors and trade contractors. The percentages can change from job to job, but the point remains: greater upfront input means fewer surprises later. In this business, surprises are expensive.
For vendors, it means that the engineering team completes the design with specific sets of equipment in mind. For the trades, it means leveraging their experience to mesh what works from a design perspective works on the particular job site.
The obvious downside is that you lose a certain amount of competitiveness on price. However, the few percentage points you might lose on supply costs are quickly erased by the immense benefits of getting a facility up, validated, and manufacturing sooner.
Design-assist aligns construction and engineering instead of separating them into different phases. The time saved alone on procurement and permitting can put a project ahead of the game by the time the overall engineering is finalized and the first shovel hits the ground. In many cases, design-assist results in dramatic time-savings, turning a 36-month project into 28 months.
Design-assist is steadily becoming the norm worldwide, and our region is a prime place to normalize the design-assist process and reap the benefits.
Why Boston?
Boston remains a world-class biotechnological powerhouse. Boston is also a pretty colloquial market. Most potential partners in the trades are known entities, and, given the presence of biotechnology here, they have experience in the nuances of pharmaceutical manufacturing.
Moreover, the men and women in the local municipal governments have experience in the permitting process for pharmaceutical manufacturing since they do more of it than almost anywhere else. Open communication is good advice anywhere, but particularly in the Greater Boston Region, where inspectors know enough about the industry to be wary of surprises – and suspicious of those who bring them. In the design-assist mode, the best practice is to bring the municipalities in at the earliest time – and communicate with them along the way.
The region does not have the luxury of excess greenfield space for new construction. Here, design assist provides an advantage in building teams to support constructability in brownfield and greenfield spaces. Again, having a trusted partner in your trades through design assist will get you much further and faster than a more mercenary relationship with subcontractors in a design-bid-build process.
How Design-Assist Really Moves Projects Forward
As I said, design-assist is a communication-intensive process. From the start of the project, we get all the players on the same platforms to vet design models and build schedules. If you get all those details squared away early, you can get your trusted vendors and trades to begin adding their perspectives on timetables and constructability.
For example, many modern manufacturing systems are assembled offsite and delivered as modular units. In traditional construction, the design documents do not always well illustrate accessibility for maintenance or tying in utilities. These are things trades contractors know and, despite the best of engineering design planning, often do not come to light until the modular unit is on-site, resulting in a change order.
With design assist, your trades partners review 3D models long before the modular cleanroom, for example, is delivered. As timetables are built out and delivery schedules configured, the trades have greater input on managing labor, ensuring the right people are on-site at any given time, and supporting union practices. Everyone can flag potential errors and apply their different experiential knowledge – dare I say – like a team.
The team-building even carries over from pre-construction to the job site. Under design assist, project engineers are more present, and even design engineers appear on site more regularly to field questions or concerns about design intent.
It is no secret that friction between engineers and contractors or field staff is almost a cliché in construction. The design-assist provides that skin-in-the-game that builds teams out of rivals. It is a process that cuts down on the tension by heading off any of the surprises that lead to change orders or cost overruns.
When weighing the risks and benefits, the positives will rain much more heavily on the side of design-assist almost every time.
For decades, the pharmaceutical industry has embraced the need to accelerate the path from bench to bedside, as they often said. The benefits are enormous, whether we are talking new vaccines or CAR-T therapies – these technologies were all fodder for hopeful academic press releases a decade or two ago.
The engineering and construction industry has become the rate-limiting obstacle between FDA approval and clinical medicine. It is far time we shook off the old way of doing things and got out of the way of progress. Design assist is the process. Boston is the place.