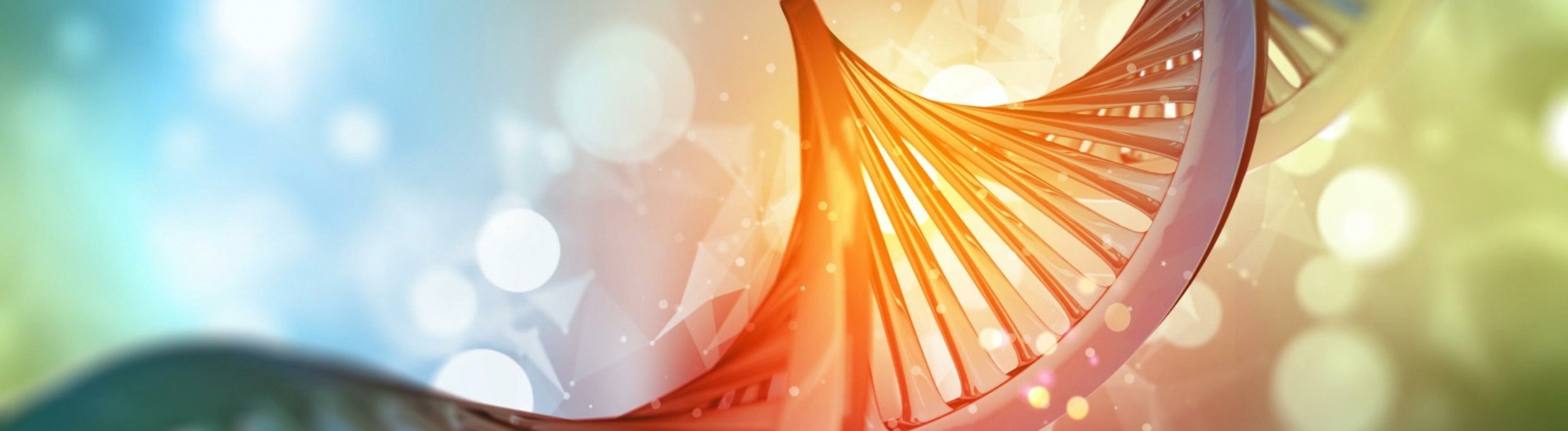
By Raymond Szuszkiewicz
The advancements in cell and gene therapy solutions and growth of biotech have given rise to hundreds of new startup companies. Companies scaling up and occupying their first facility are hit with a daunting task: how do I go about constructing a facility?
Learning Objectives
- The growth of the biotech industry has jumpstarted the rise of new startup companies. The next steps of starting construction have prompted questions on how to start building a facility.
- The layout of a facility (e.g., column spacing, floor-to-ceiling height, square footage) can make it easier to decide how to move forward with space planning or showcase potential challenges of dictating a floor plan.
- Learning from the past can help to avoid future mistakes. Ensuring a building can meet your current and future needs is essential and prioritizing gathering all information before you buy a building can save you time and money.
Analytics insights
There are several factors to look for that are essential when planning to buy or build a new facility. From general layout of the space to considering what the type of building you are constructing needs are important factors to contemplate in order to be efficient and adaptable. Building from scratch and buying an existing facility have different requirements that should be met. An existing facility can cause a buyer to face more challenges due to limitations of a pre-engineered structure.
While new construction is generally more expensive, an existing facility may bring about unforeseen costs if it does not have the flexibility to meet the needs of a certain type of building. Factoring in what is most cost-effective in the long run and considering potential changes or upgrades a facility may need is recommended.
What to look for?
Span and floor to bottom of beam height
Having a large span between columns is helpful for space planning and makes future alterations easier. The open plan allows the process to dictate the layout.
A good floor-to-floor height, or floor to bottom of the beam, is important for classified cleanrooms with walkable ceilings. Take your average manufacturing ceiling height and add 13 feet to the bottom of steel to provide adequate walking clearance under ductwork and utilities. Anything lower typically leads to a difficult to navigate, crawlable ceiling. If you anticipate a large number of high-hat areas, you may want to consider adding 13 feet to those high points if the project can afford it. Otherwise, careful consideration will need to be paid to determine how to gain access to your lights, high-efficiency particulate air (HEPAs), and other items in the ceiling.
If you’re purchasing an existing building, stick to one designed for factory industrial applications. Trying to turn an office building into a manufacturing site will create design challenges, lengthen the project schedule and eliminate the savings you hoped to make by purchasing something cheap. And you’ll be left with a building that is harder to manage and less adaptable to change.
How much square footage do I need?
It depends on what you’re manufacturing and many other factors, but here are some ballpark starting points:
- Non-Virtual Research-Based Startup Companies: 1,500 square feet to 15,000 square feet
- Research + Preclinical: 10,000 square feet to 40,000 square feet
- Research + Preclinical + Clinical: 50,000 square feet to 75,000 square feet
- Clinical + Commercial: 90,000 square feet to 150,000 square feet
New construction vs. existing fit-out
- New construction is typically more expensive. The cost savings experienced when fitting out an existing building translates to reduced flexibility. But if you purchase the right existing building that meets the needs of your project you can benefit from the cost savings without making compromises.
- On your search for an existing site, it is helpful to have a rough design in hand so you know the property can meet your needs. Confirming the square footage needed can avoid regrets and, in most cases, will save you money in the long run.
- Purchasing an existing property that wasn’t meant for your specific use can require a large number of upgrades. Do you need to upgrade the electrical service coming into the building? Are drain piping, domestic water service, and fire protection water service diameters large enough or do you need to replace underground piping? If you do need to upgrade, then you’ll need to factor in the cost of the trenches or potentially demolishing and replacing the entire slab if it’s cost-effective to do so.
- Is there a vapor barrier under the slab? If not, you may have to demo the slab and repour. Otherwise, any water coming through the slab can make bubbles appear in the epoxy flooring in your new cleanrooms.
- Exposing a wall or roof cavity means you need to upgrade it to meet current energy codes. Make sure the contractors are aware of this requirement and they don’t open up any walls without the intent to upgrade them.
Adequate lot size
- Parking – Do a quick parking calculation based on your anticipated building size. Designing a multistory parking structure is very expensive, and a large majority of the footprint will be dedicated to ramps and car circulation. Parking structures should only be used for extremely large facilities in areas where land costs are very high.
- Fire truck access road – Look into access road requirements but plan to have a loop around the building to be on the safe side.
- Truck turning radii – Show the truck turn arounds and turn radii on the plan to ensure adequate space is provided.
- Equipment outside building – Along with sizing the lot to accommodate parking, dedicating space for exterior equipment (transformers, generators, and trash & cardboard compactors) should also be taken into consideration.
Future expansion
- Look for opportunities on the site to expand, whether it’s dedicating space on your land, or researching whether a neighboring property is likely to sell.
- Think about how the future expansion can be constructed without affecting existing operations.
Location
- Realize that sites like Boston come at a premium. While other major cities in the US can potentially be 15% cheaper. Look at Arcadis’ Annual International Construction Cost Index to help you site your project.
Pre-engineered buildings
While they are a wonderful product with a variety of great applications and many benefits (such as the large column spans), they also can create some challenges. The root cause of this is they are often designed to meet minimum standards of construction depending on their original intended use.
Roof structure:
- The steel supporting the roof usually doesn’t have enough extra capacity to hang the walkable ceiling you want for your clean rooms. Hanging isn’t the only option; you can use deep stud walls and light gauge members to support the ceiling. But if you only planned for 2-inch modular panels in your preliminary design, all these fat walls could present a problem. Also, if your rooms are very large and the spans are too wide for light gauge studs, then you’ll need a secondary steel structure to support the walkable ceiling. And new steel means new footings, which means cutting more holes in the existing slab.
- Along with not being able to support your walkable ceiling, you might have some trouble supporting ductwork, piping, etc. from the roof structure. You’ll need to post down to the level below to support them.
- And if you can’t support these items, you can rule out having air handlers or other large equipment on the roof without adding a separate support structure, so you’ll need to find space inside the building or elsewhere on-site for that equipment.
Exterior walls:
- Many pre-engineered buildings are constructed with flimsy skin with few support points, so modifications down the road could be challenging.
- Try and get extra panels if the vendor still makes them in case you need to infill them in the future.
- You are also less likely to get high-level LEED certification depending on the R-value of the components.
Adding equipment platforms:
- The columns in pre-engineered buildings typically don’t have enough capacity to support a new equipment platform, so new columns will likely need to be added.
Slab:
Some pre-engineered buildings have hairpin rebar on the columns along the perimeter. You cannot touch the slab in these areas, so all your piping needs to be diverted around it or above it.
All of these points translate to more design time to find solutions to problems that wouldn’t exist in a wide-flange building that has larger tolerances built-in. Weigh the pros and cons of each building before making your decision.
Sloped site:
- Cut and fill isn’t too expensive but removing excess soil off-site can be. Grading the site for parking and truck movement typically involves removing a large amount of soil removal.
Small footprints and multistory manufacturing
-
Multistory could lead to a reduction in footsteps with an efficient design. However multistory requires material elevators, typically two: waste and materials & product. Consider the locations if these are existing elevators. The design will either need to be tailored around the elevators, or they may need to be demolished if the location is hindering other key adjacencies. And please remember, there are no truly “clean” elevators. Elevators should be kept within your computer numerical control (CNC) circulation and should not be used in Grade D areas or higher.
Landlord
- Having a landlord requires a lot of back and forth to get approvals. This can be time consuming and could prevent you from meeting your schedule demands. Does your loading dock meet their desired aesthetics? They will ask to see truck schedules and much more information to keep their other tenants happy. Are you allowed to put air handlers on the roof? Are exhaust stacks visible from the street? What screening do they require? Chances are it’s not cheap, and you’ll need more design hours to do site-line analysis and renderings to present to them. Some of these requirements could make your project unachievable or could kill a future alteration/addition.
AHJ requirements
- It would be beneficial to schedule a friendly meeting with the local Authority Having Jurisdiction (AHJ) and review your goals. They can tell you upfront what challenges you’ll face. Can a new road to the site be created for truck access? Is there a list of allowable materials that can be seen from the road? For example, some jurisdictions don’t allow a chain link fence to be seen from the street.
- If the code says you will need 300 parking spaces, but you’ll never have more than 75 people on site, what steps need to be done to prevent you from constructing ~200 unused parking spaces that only contribute to the heat island effect and permeable surface on-site? You shouldn’t rely on the AHJ to grant variances, but many AHJs are flexible when it comes to a legitimate hardship.
Environmental study
This is less likely to be an issue for you, but there are many sites that carry restrictions based on environmental protection. It’s important to verify if your site has any and how they will affect your project.
- If you have protected wetlands nearby, you should see what restrictions you have and map them on the site to see what your buildable area is and where you’re allowed to locate equipment.
- Before you purchase a brownfield site, investigate the costs of removing contaminated soil, abandoned tanks, etc. You can get grants and other assistance from entities like the environmental protection agency (EPA) if you choose to occupy a brownfield, but the benefits should be weighed with the challenges.
Key takeaway
Every company has lessons learned from prior projects, don’t let your startup repeat the same mistakes. Don’t buy a building before you know what will go into it. Perform a quick engineering study to ensure your building will be able to meet your needs. This will save you time and money in the long run.
This article originally appeared on Consulting-Specifying Engineer